HOW MOLECULAR BORIC ACID CHEMICALLY REACTS WITH METAL TO FORM A BORON-OXIDE LOW FRICTION PROTECTIVE BARRIER
Boron is a chemical element with the symbol B and atomic number 5. Boric acid is found mainly in its free state in volcanic districts. It is also found as a constituent of many naturally occurring minerals.
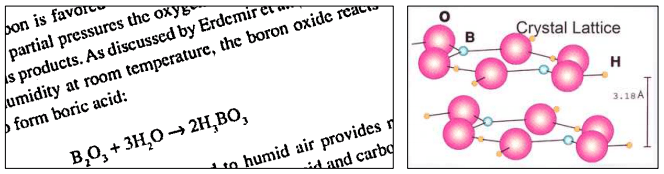
Boric acid and its salts are found in seawater, in plants, including almost all fruits. Boric acid is often used as an antiseptic, insecticide, flame retardant, or precursor to other chemical compounds. It has the chemical formula H2BO3 and exists in the form of colorless crystals or a white powder that dissolves in water.
However, boric acid is not soluble in petroleum (mineral or synthetic); thus it is characteristically not soluble in motor oil. Initial tests by the Argonne National Laboratory combined the larger boric acid particles with pure poly-alpha olefin, the principal ingredient in many synthetic motor oils. While these larger particles dramatically improved the lubricity of the pure oil, within a few weeks gravity had started to separate the mixture. Ali Erdemer at the Argonne National Laboratory, together with Advanced Lubrication Technology (ALT), developed the means to emulsify individual boric acid molecules in a primary fluid carrier. These two chemicals combined are registered as Boron-CLS-Bond®, a primary carrier and molecular boric acid.
There is a limit to how much boric acid that can be emulsified into the primary carrier. For the different MotorSilk® and LubriSilk® applications ALT also adds other superlative fluids into the formulations to enhance the performance of the product for specific uses. This is done in a very calculated way, as adding another fluid reduces the amount of Boron-CLS-Bond® that can be put into that product. So, based upon the product, how it is going be used and what it is supposed to do, the maximum amount of Boron-CLS-Bond® is adjusted to an amount that is highly effective, yet is combined with other high performance factors from the supplemental fluids. All of these fluids have to be compatible with each other, presenting a formulation challenge that has several patents.
The result is that, with Boron-CLS-Bond®, the boric acid is introduced into motor oils and lubricants as a miscible emulsion of boric acid molecules, each molecule less than 0.5 nanometers in size. These boric acid molecules are distributed throughout the engine or application parts within the carrier oil, and react with all the metal surfaces. When the product is introduced into equipment there is a chemical ‘covalent’ reaction between the molecular boric acid and the host metal(s), creating a near permanent new surface that is harder than the original surface at 85% hardness of a diamond (Rockwell 85). A covalent bond, also called a molecular bond, is a chemical bond that involves the sharing of electron pairs between atoms. These electron pairs are known as shared pairs or bonding pairs, and the stable balance of attractive and repulsive forces between atoms, when they share electrons, is known as covalent bonding.
When multiple molecules combine, by way of some of their elements sharing electrons with an element of another molecule, it creates an entirely new molecule, usually with different properties (from minor to very significantly different properties). These bonds are very strong. So, when Boron-CLS-Bond® is added to metal it will generally react in this manner with all the metals with which it comes in contact, to form a new surface boron-oxide (boroxide, B2O3) barrier to each metal part. The precise resulting metal and boron molecule chemical name will depend upon the substrate metal with which the boric acid reacted. However, we generically call these covalent bond chemical reactions the creation of a “metallic boroxide”.
The covalent formation of metallic boroxide creates a new metal surface that becomes an integral part of the engine or metal parts, harder than the original, that is chemically resistant to acids (corrosion and all contaminants) and has very high wear resistance. This barrier surface is very strong and in an engine will typically remain part of the engine surface through approximately 3,000 hours of run time or approximately 160,000 kilometers of distance traveled. An initial engine treatment of Boron-CLS-Bond® is designed to introduce approximately 30,000 ppm of boric acid containing approximately 5,000 ppm of Boron per the formula H3BO3. The initial reaction with the metal surfaces will immediately use approximately 60% of the boric acid in the creation of this protective barrier.
Most of the balance of the free boric acid molecules will, through a process of ionic (electromagnetic) attraction, form a crystalline lattice of boric acid molecules, which macromolecule bond together as boric acid crystalline platelets. Under an electron microscope these look much like a deck of playing cards. The creation of these platelets uses up approximately 35% of the boric acid initially introduced into the engine or an amount about 10,500 ppm of boric acid/1,700 ppm boron. These 200 to 300 nanometer thick platelets, through Van Der Waal forces, align along any axis of movement in the engine and ionically bond to the new metallic boroxide surfaces. The platelets ride over each other with virtually zero friction and thus allow the metal surfaces to benefit from this extremely low friction coefficient (usually about a 90% reduction in friction between the metal surfaces).
This technology is self replenishing, in that at any point where the metallic boroxide surface experiences severe abrasive action and is abraded off the metal substrate, the boric acid in the platelets and/or any residual free boric acid in the system will almost immediately repeat the reaction with the metal and re- establish the metallic boroxide barrier. The abraded metallic boroxide does not disappear, and in the presence of oxygen, and moisture (hydrogen) is broken down into boric acid and then is again ready to bond with any part of the metal that has not already reacted with Boron-CLS-Bond®. Any free boric acid in the system will fill in any open spots in the platelets and thus there is minimal impact to the boric acid lubricating regime, with only a small reduction in the free boric acid dispersed in the system.
In a fully closed system, the benefits will last an extraordinarily long time, the limiting factor being the life of the lubricant fluid to which Boron-CLS-Bond® was added. In a semi-closed system, such as an engine, the metallic boroxide will still perform even after about 20 oil changes, because much of the free boric acid stays in the engine due to chemical attraction, although may start to decline slowly if there is not enough free boric acid to replenish any abraided platelets. No other lubricant in the world can last for the time or distance represented by 20 oil changes. Boron-CLS-Bond® improves the other lubricants longevity because it can last far longer than they can, and makes the operating conditions much easier for the lubricants.
In an open system such a fuel system, the benefits last a shorter time because the residual free boric acid rushes through and out of the system, which is why it is recommended to add a slight amount continuously (1:1000 or even 1:2000, blended with the fuel) to keep the Boron-CLS-Bond® barrier and platelet creation intact, so that the fuel pumps and injectors receive replenishment. At the end of the extended usage periods, a new treatment should be performed, or during the use period, small treatment amounts should be added to maintain the full functionality of the lubricating benefits.
In summary, Boron-CLS-Bond® creates a boundary layer on metal surfaces as a highly protective, low friction solid boundary later, acting as a surface coating and protector, as well as a cleaner. The coefficient of friction is further reduced with platelet action and the remaining free boron circulates as a standby to react wherever it may be needed, while enhancing the operating conditions of the existing lubricant.